Abrasive CNC Waterjet cutting systems are flexible in the processing of a wide variety of profiles and a nearly-unlimited variety of materials.
Cutting is extremely precise without thermal effects on the material. Cold cut edges created during cutting with an abrasive CNC waterjet cutting machine are free of burrs and structural impairment.
An important benefit of the abrasive CNC Waterjet cutting machine is the ability to cut material without interfering with its inherent structure, as there is no ‘’heat-affected zone’’ (HAZ). Minimising the effects of heat allows the metals to be cut without harming or changing intrinsic properties. The heat transfer during laser, plasma, and torch cutting changes the structure. The edge melts and burrs are formed.
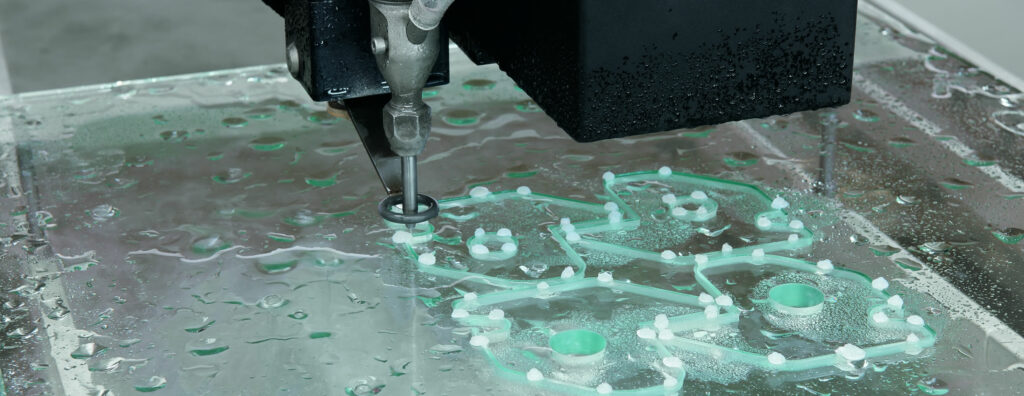
How Waterjet Cutting Works
Our Waterjet cutting machine, the Byvision Pro, allows us to accurately and precisely cut a wide range of materials to very tight tolerances. Our Waterjet cutting process is achieved by carefully mixing a very hard garnet with water pressurised to approximately 60,000 psi. This garnet and water mixture is then forced through a tungsten carbide focusing tube with an orifice diameter of 0.8 mm. The stream of abrasive and water mixture then effectively cuts through the material on the bed of the machine.
ByVision Pro
The ByVision Pro is the CNC waterjet cutting system of choice for unmatched productivity, performance and efficiency, ensuring accuracy and quality of your components.
Parameters such as cutting speed, pressure and quantity of garnet are infinitely adjustable and are continuously adapted to the material and the shape of the contour. Each part can be assigned many different parameter sets. The shuttle table enables safe access to the cut parts, which are cleaned automatically during the table change. Set-up times and loading and unloading during the cutting process are minimised, increasing productivity and economic efficiency.
Water jet cutting is considered a “green” technology
CNC waterjet cutters produce no hazardous waste, which saves you time and money. They can cut off large pieces of reusable scrap material that might have been lost using traditional cutting methods. Parts can be closely nested to maximise material use, and the CNC Waterjet cutter saves material by creating very little kerf. So reducing the per-unit cost of subcontract components.
CNC Waterjet cutters use very little water, and the water that is used can be recycled for other applications within our manufacturing site. Waste water usually is clean enough to filter and dispose of down a drain. The garnet abrasive is a non-toxic natural substance.
The ByVision Pro waterjet at Waterjet Precision UK Ltd produces components in a clean low noise environment and eliminates airborne dust particles, smoke, fumes, and contaminates from cutting materials which can be characteristic of plasma and laser cutting. This both greatly improves the quality of precision components and the work environment.
Process Benefits
Cold cutting without thermal influences
Flexible and precise processing of nearly all materials
No tooling required
Maximum material usage thanks to minimal, burr-free, part interspacing and part-in-part (nested) production
No costs for tooling storage
Stress free processed parts due to multi-head and multi-layer cutting
Materials and Industries
The versatility of our abrasive CNC Waterjet cutting machine allows it to be used in nearly every industry. There are many different materials that can be waterjet cut. Some of them have unique characteristics that require special attention when cutting. Each material cut will have some distinct characteristics that have to be taken into account.
A nearly endless variety of materials up to approximately 200mm thick can be Waterjet cut depending on the quality and composition of the material.
Common materials which we work with include:
- Stainless steel, aluminium, titanium, non-ferrous, and other metals;
- Carbon Fibre;
- Hard and soft foam;
- Sandwich and structural materials;
- Stone, including granite and marble;
- Ceramics, glass and bullet-proof glass;
- Synthetics, including thermoplastics, and duro plastics;
- Fibre reinforced synthetics, and reinforced plastics; and
- Sealing Materials, including rubber and fabric based laminates.
Areas of Application
- Automotive industries
- Machine and apparatus engineering
- Architectural/Design
- Agriculture
- Chemical industry
- Electronics industry
- Aerospace
- Construction and interior fittings
- Food industry
- Medical engineering
- Signage and logos
- Glass industry
- Boat building
The only materials that cannot be cut with waterjet are tempered glass, diamonds and certain ceramics.